In today’s world, the DIY culture has gained immense popularity, allowing individuals to express their creativity while promoting sustainability.
Have you ever thought about making your own paper cups? In this blog, I will guide you through the exciting process of creating paper cups using Get Bio Pak’s advanced automatic machines.
To create your own paper cups, you need to gather specific materials, understand the machine’s functions, and follow a series of detailed steps to produce high-quality, customized products.
The Importance of DIY Culture
DIY culture is more than just a trend; it represents a shift towards personalization and sustainability. People are increasingly interested in creating unique items that reflect their style and values. This movement encourages creativity and resourcefulness, allowing individuals to take control of their consumption habits.
At Get Bio Pak, we embrace this DIY spirit by providing the technology and support needed for anyone to craft their own paper cups.
Our automatic machines simplify the process while ensuring high-quality results. This guide will equip you with the knowledge to start your journey into DIY paper tea cup production.
Preparing for Your DIY Project
Before diving into the production process, it’s essential to gather the necessary materials and understand their characteristics.
Required Materials
- Paperboard: Choose high-quality paperboard sourced from sustainable forests. Look for a thickness of 0.3 to 0.5 millimeters for optimal strength.
- Coating Material: Select biodegradable coating options like water based barrier coating (WBB) instead of traditional polyethylene (PE). WBB provides excellent water resistance without compromising environmental integrity.
- Food-Grade Inks: Ensure that the inks used for printing are safe for food contact. These inks should comply with safety regulations.
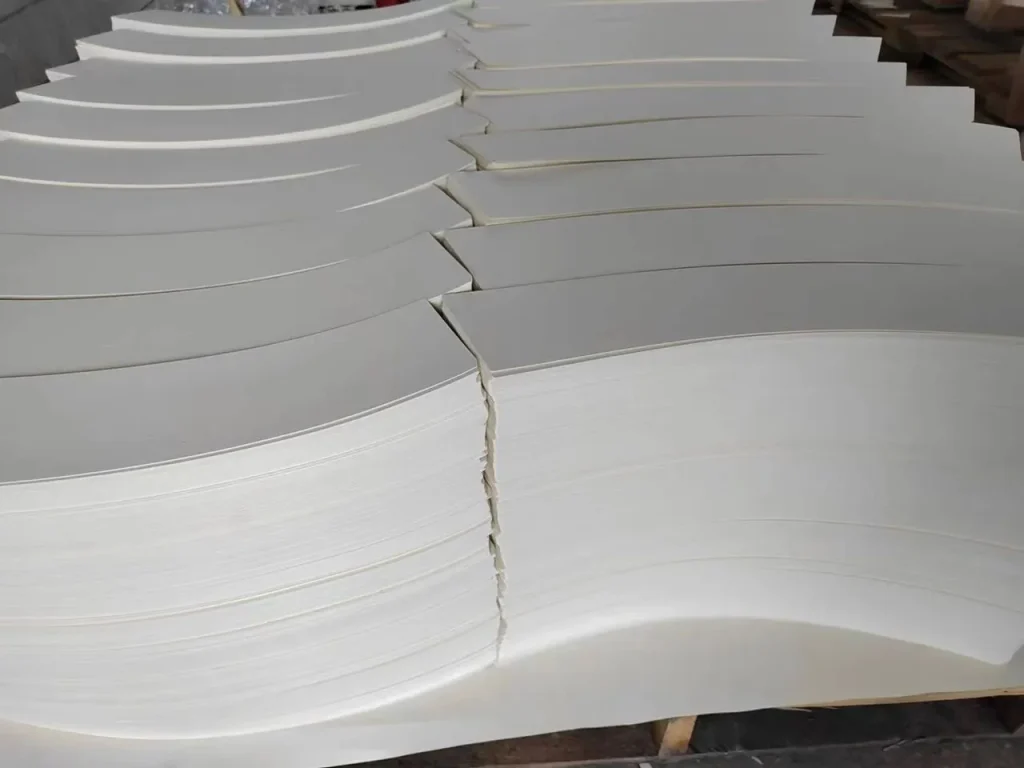
Tips for Choosing the Right Paper
- Consider Usage: Identify whether your cups will hold hot or cold beverages. This will influence your choice of paperboard and coating material.
- Check Certifications: Look for certifications that guarantee the sustainability of your materials, such as FSC (Forest Stewardship Council) certification.
Understanding Get Bio Pak’s Automatic Machines
Get Bio Pak‘s automatic machines are designed to streamline the cup-making process while maintaining quality and efficiency, every part perfected well setted in blind rivet manufacturer.
Machine Functions and Interface
- User-Friendly Interface: Our machines feature an intuitive interface that allows users to easily set parameters for different cup designs.
- Versatile Capabilities: The machines can handle various sizes and styles of cups, making them ideal for custom projects.
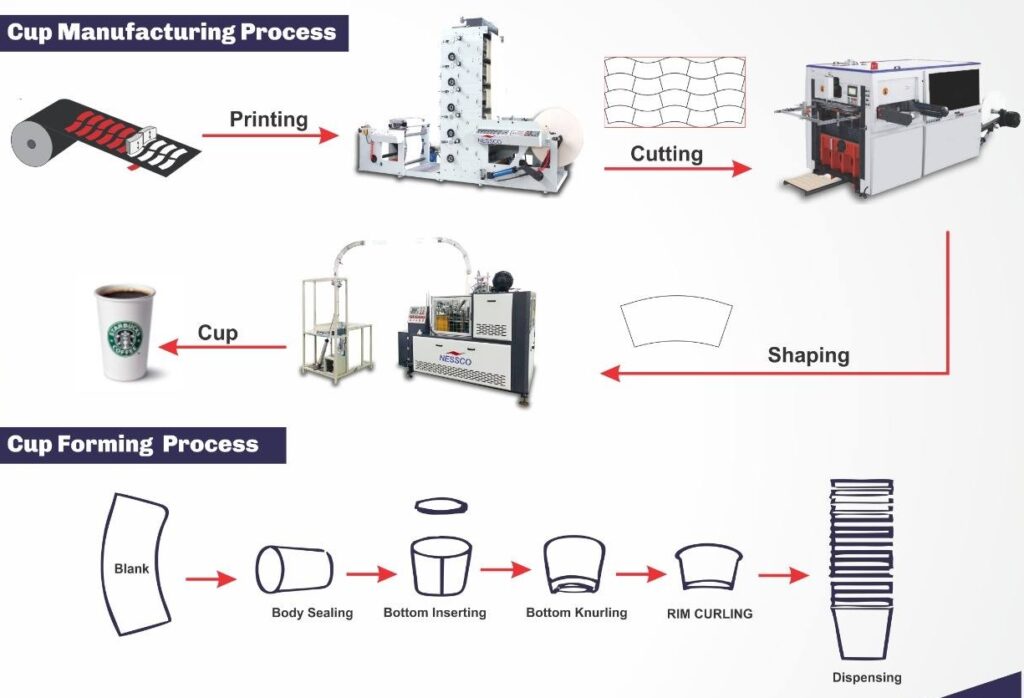
Common Questions and Solutions
- What if I encounter a malfunction? Regular maintenance checks can prevent most issues. Consult the user manual for troubleshooting tips or contact our support team for assistance.
- Can I adjust production speed? Yes, our machines allow you to modify production speed based on your requirements, ensuring optimal efficiency.
Detailed Production Steps
Now that you’re prepared, let’s dive into the step-by-step process of making your own paper cups.
Step 1: Prepare and Cut the Paper
Start by cutting your paperboard into appropriate sizes for cup formation.
- Cutting Equipment: Use a precision cutting machine to ensure clean edges without any burrs.
- Pre-Treatment: Flatten the paperboard and pre-score it if necessary to facilitate easier folding later on.
Step 2: Set Machine Parameters
Adjust the machine settings according to your design specifications.
- Design Input: Enter the dimensions and specifications of your desired cup design into the machine’s interface.
- Coating Selection: Choose the appropriate coating material based on whether you need hot or cold beverage cups.
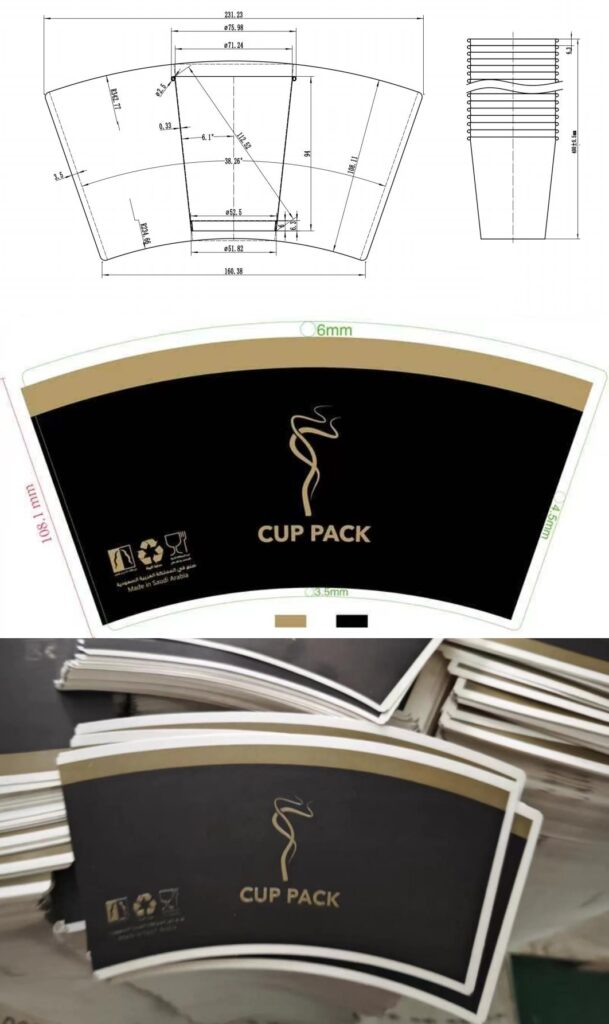
Step 3: Start Production and Monitor Quality
With everything set up, it’s time to begin production!
- Production Monitoring: Keep an eye on the machine as it operates. Ensure that each step is executed correctly from forming to sealing.
- Quality Checks: Periodically inspect cups during production for any defects or inconsistencies in sealing or printing.
- Printing on Paperboard: The visual appeal of a paper cup plays a vital role in branding and consumer recognition. We employ flexographic or offset printing methods to apply vibrant designs and logos onto the paperboard before it’s cut into blanks.
- Adhesion Checks: Ensuring strong ink adhesion is critical for maintaining design integrity throughout subsequent processing stages.
- Cutting Paper Cup Blanks: The cutting stage is essential for creating precise shapes necessary for forming cups.
- Accurate Cutting Equipment: Our cutting machines ensure clean edges without burrs, which could lead to leaks or structural weaknesses in the final product.
- Waste Management: We prioritize minimizing material waste during this process by implementing efficient cutting techniques.
- Forming Paper Cups: This stage transforms flat blanks into functional cups.
- Cup Shaping: The blanks are placed into forming machines that fold and seal them into cylindrical shapes using heat sealing or ultrasonic technology.
- Bottom Attachment: The bottom of each cup is securely attached through precise sealing techniques to prevent leaks.
- Rim Curling: Rim curling enhances both functionality and user experience.
- Creating a Smooth Rim: This process involves curling the top edge of the cup to create a rounded rim, which reinforces strength and allows lids to fit securely.
- Bottom Sealing: Bottom sealing is crucial for ensuring leak-proof performance.
- Sealing Techniques: We utilize heat sealing or ultrasonic sealing methods to securely attach the bottom of each cup to its body, ensuring durability during use.
Step 4: Post-Processing and Packaging Techniques
After production, it’s crucial to handle your cups properly before they reach consumers.
- Final Quality Control: Conduct thorough inspections on completed cups. Check for leaks, print quality, and structural integrity.
- Packaging Solutions: Use eco-friendly packaging materials to maintain hygiene and protect your cups during transport.
- Food-grade conveyor belts play an important role in the inspection and sorting process. These belts help transfer the cups smoothly to the inspection station, where each cup is carefully checked for leaks, printing errors, and structural integrity issues.
Uses and Creative Applications
DIY paper cups can be utilized in various settings, making them versatile additions to any event or occasion.
Event Applications
- Parties: Customize cups with unique designs that match your event theme. They serve as great conversation starters!
- Corporate Events: Use branded cups at conferences or meetings to enhance brand visibility while promoting sustainability.
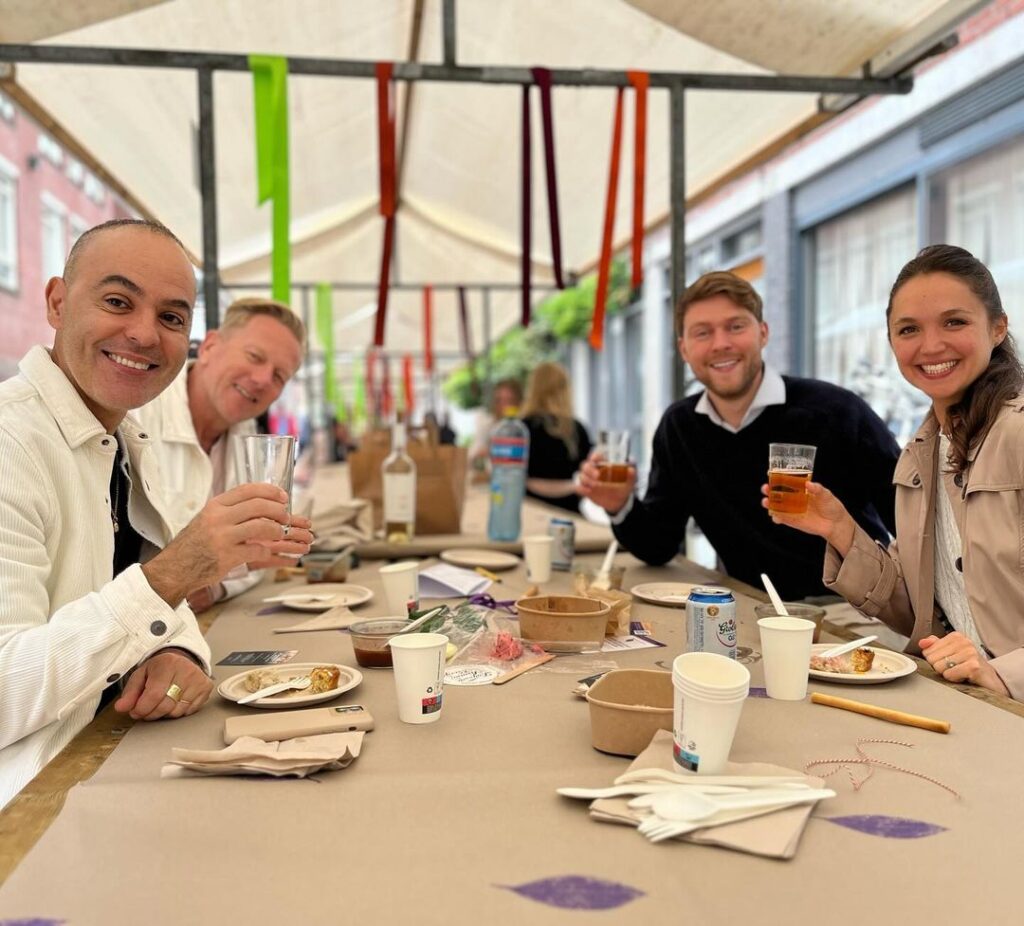
User Feedback and Success Stories
Many users have successfully implemented our technology in their projects. Here are some inspiring stories:
- A local café started using custom-designed cups made from biodegradable materials, attracting environmentally conscious customers who appreciate sustainable practices.
- An event planner created themed cups for weddings, impressing guests with personalized designs that added a special touch to the celebrations.
Conclusion
Creating DIY paper cups using Get Bio Pak’s automatic machines is not only fun but also rewarding. You gain control over your product design while contributing positively to environmental sustainability. I invite you to share your creations with us! Your innovative ideas can inspire others in their DIY journey.
FAQ
What types of materials are used in making paper cups?
Paper cups are primarily made from high-quality paperboard sourced from sustainable forests. They are coated with biodegradable materials like PLA or traditional PE for water resistance. Food-grade inks are used for printing designs safely on the surface.
How does Get Bio Pak’s machine enhance production efficiency?
Our automatic machines streamline production by automating cutting, forming, and sealing processes. This reduces labor costs while ensuring consistent quality across all produced cups, making it easier for businesses to scale their operations effectively.
Can I customize my paper cup designs?
Absolutely! Our machines allow you to input specific dimensions and designs tailored to your needs. You can create unique branding opportunities or personalized designs for events while ensuring compliance with food safety regulations.
What measures are taken for quality control during production?
Quality control involves rigorous inspections at multiple stages—checking for leaks, print alignment, structural integrity—ensuring each cup meets safety standards before packaging and distribution. This guarantees a high-quality product every time.