Each GetBioPak quality paper cup is made with safe materials and goes through a closed production process using advanced technology. GetBioPak would like to introduce you to the most comprehensive paper cup production process in the article below:
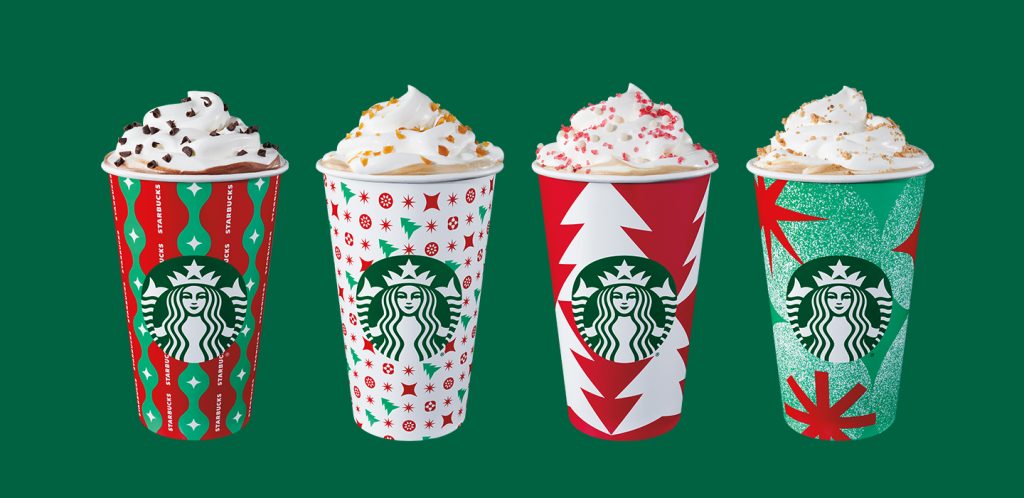
Step 1: Raw Material Preparation
Time: 1 week
Mainly Material: 100% FSC wooden pulp paper
Quality: ISO, FSC, CE Certificated
GetBioPak’s disposable paper cups are made from high-quality imported cup stock paper. This paper is made from 100% highly durable SBS (Solid Bleached Sulfate) pulp that contains no harmful substances or industrial bleach, making it ideal for manufacturing safe and eco-friendly paper cups.
Depending on the intended use, each cup stock paper roll is coated with 1 or 2 layers of PE, which helps increase waterproofing and heat resistance while ensuring safety standards for consumers with hot or cold drinks.
To fit the intended use and cup designs, GetBioPak currently offers 1PE coated paper cups in sizes ranging from 3 to 22 oz, and 2PE coated paper cups in sizes ranging from 12 to 22 oz.
Step 2: Choose the Correct Weight Paper
Paper weight determines the strength and resistance of the paper to deformation. The weight of GetBioPak’s paper cups ranges from 170gsm to 320gsm, depending on the volume of each type.
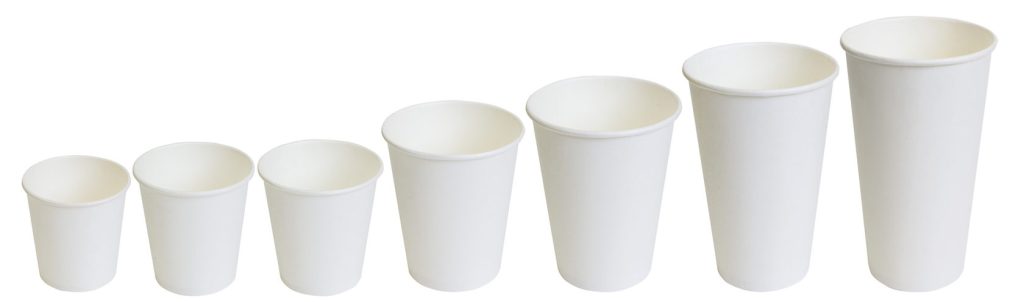
Step 3: Printing Conspicuous Customized Design
Time: 1 week
In the paper cup production process, GetBioPak currently employs offset, silk screen, and Flexo printing techniques. Paper die-cutting and paper cup-forming processes vary according to printing methods.
- Offset printing
The paper will be cut into individual sheets before being sent to the offset printer. When the printing is finished, the sheets will be fed through the roll-forming machine before being fed into the paper cup-forming machine.
The benefit of this technique is the quick printing time; it can complete up to 90% of the logo and is suitable for complex prints. As a result, paper cups with offset printing are an excellent choice for those seeking to establish consistent brand recognition.
- Flexo printing
The paper roll is fed into the Flexo printer, then passed through the roll forming machine, and transferred to the paper cup forming machine in the paper cup production process using the Flexo printing technique.
Flexo printing is a technique of embossing on the surface of materials, creating impressive and unique paper cups. This technique can print at a high speed of 700m/min.
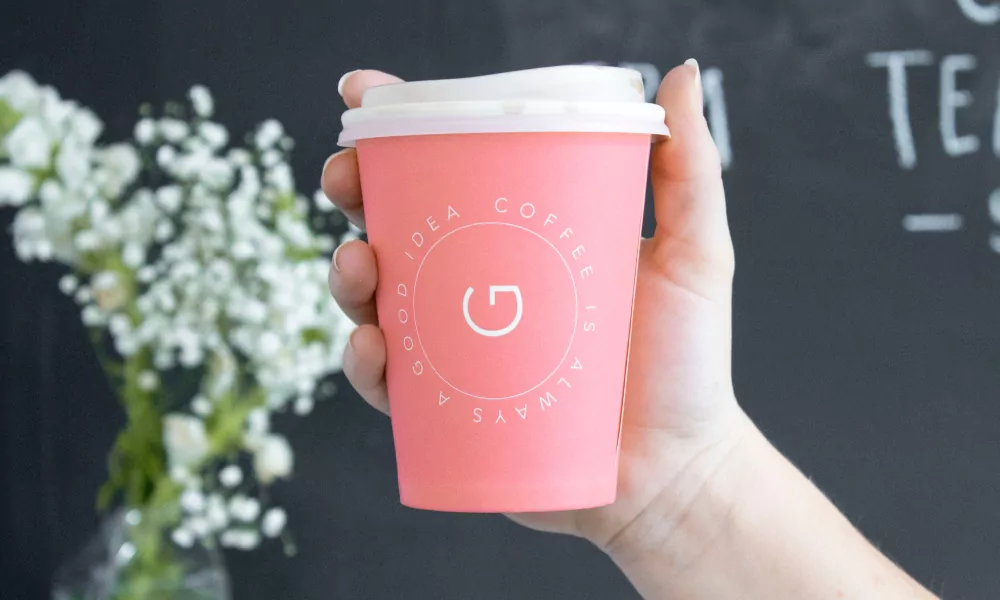
- Silk screen printing
The paper roll will be fed into the roll-forming machine, which will then feed into the paper cup-forming machine. Following the formation of the cups, they will be transferred to be silk screen printed and dried.
Silk screen printing is a simple and low-cost printing method. This technique, however, should only be used for logos, single-color images, and simple textures. Silk screen printing is done on pre-formed paper cups.
Step 4: Die cutting
To make paper cups, cut the printed paper sheet into fan-shaped sheets using a flat indentation and cutting machine (also known as a die-cutting machine).
Step 5: Cup Forming
Time: 1 week
The operator only needs to feed the fan-shaped paper cup sheet and the cup bottom roll paper into the feeding port of the paper cup forming machine, and the machine will automatically form the paper, seal, punch the bottom, and perform other operations to form what you require. Paper cups in various sizes. One person can easily operate the entire process

Step 6: Check and Inspection
The completed paper cup will be transferred to the inspection department. Quality paper cups must meet the following criteria: a sturdy bottom, high adhesion, no smudged ink on the cups, eco-friendliness, and consumer safety.
GetBioPak uses soy ink in the printing process on each paper cup. This is a food-grade ink that contains no metals, meeting the Ministry of Health’s food hygiene and safety standards.
All standard paper cups will be sorted and stacked in a predetermined number. They will then be carefully packed in order to avoid contamination during transportation.
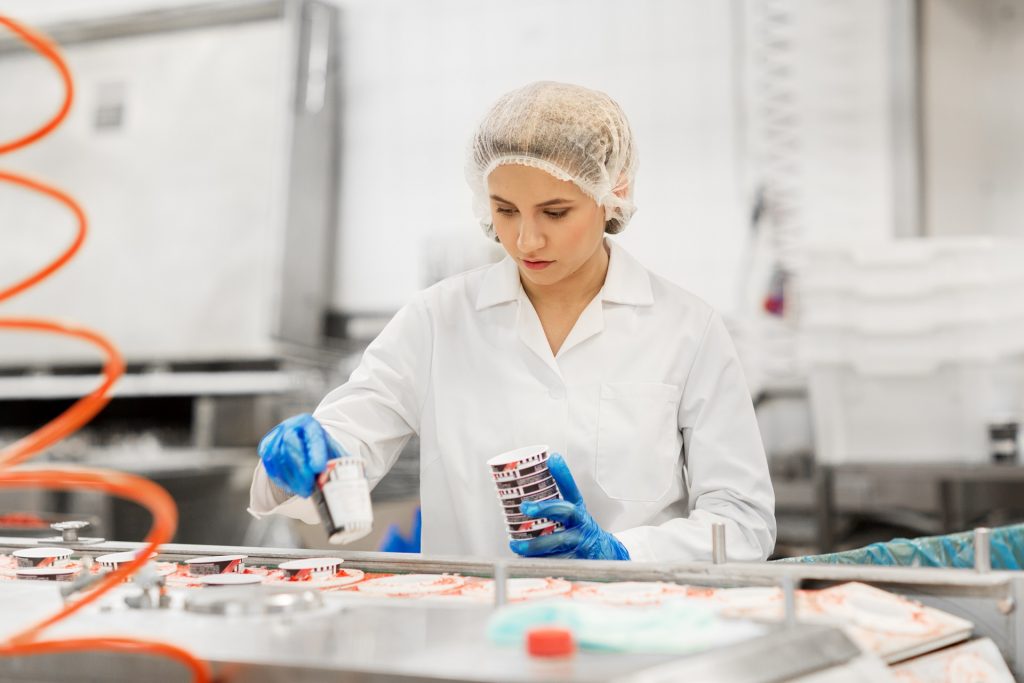
Step 7: Packing
Seal the finished paper cups in plastic bags, and then pack them into cartons.
Not only has GetBioPak become a partner of many F&B corporations such as Starbucks, Costa, Peets Coffee, Subway, Dunkin’ Donuts, etc., but we also export our products to the US market.
For order-related questions or consultation, please contact us via our Hotline: 0086 19884182202